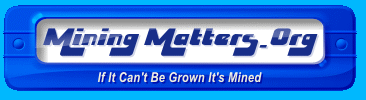
Home Sawgrass Reclamation Fact or Fear Flambeau Mine Restoration Educational Resources Mining Machines at Work More Success Stories Photos Luscar Mine Canada Mining Trvia Common Minerals Action Alerts Environmental Opinon’s Talking Points Stay Out – Stay Alive
Modern Mining Machines at Work
COAL MINING
Coal is mined by two general methods: surface mining and underground mining. In general, surface mines extract coal deposits located up to 30 m (100 ft) below the surface, while underground mines excavate coal beds further underground.
A. Surface Mining
In surface mining, or strip mining, earth–moving equipment is used to remove the rocky overburden and then huge mechanical shovels scoop coal up from the underlying deposit. The modern coal industry has developed some of the largest industrial equipment ever made, including shovels (part of a piece of equipment known as a dragline) capable of holding 290 metric tons of coal.
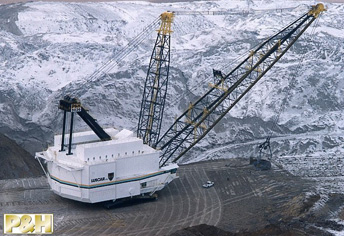
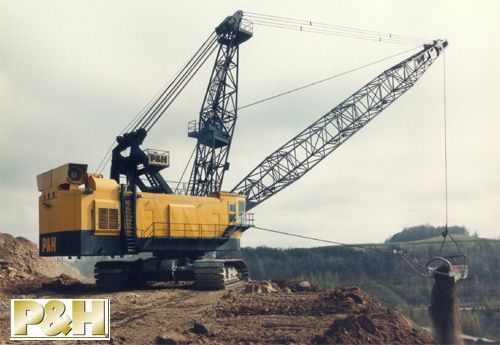
Pictured above are a P&H 9020 walking dragline (left) with a P&H 2355 crawler dragline on the (right). You can see each step of the erection of a P&H 9020 from Start to Finish Click Here.
Click on photos for more descriptions about the machines
A-1 Open Pit Mining
B. Underground Mining
Detailed illustration with description of an Underground Mine
To reach coal beds deeper than about 30 m (about 100 ft), miners typically dig underground mines. Two or more shafts are tunneled down into a coal seam—typically, different shafts are used for the passage of miners and machinery and for the passage of mined coal. There are three types of underground mines—shaft, slope, and drift mines. The type excavated in a particular case depends on the depth of the coal deposit, the angle of the coal bed, and the thickness of the coal seam.
Shaft mines are dug to reach deep coal beds, usually about 200 m (about 660 ft) or more below the surface. A shaft mine uses two vertical shafts to reach the coal bed. Slope mines reach coal deposits that have been distorted or tilted by shifts in the earth’s crust. A slope mine uses two angled shafts to reach the coal bed. The passageways of a slope mine typically begin where the inclined coal bed outcrops on the surface and follow the incline into the ground. Some slope mines angle down through the overburden to reach the sloping coal bed, then parallel the bed into the earth. If the grade of the slope mine passageway does not exceed 18°, the coal is usually transported from the mine by conveyor. For steeper grades, coal is typically removed by trolley or mine cars.
Drift mines are used in cases where a coal seam outcrops on a hill or mountainside. A drift mine consists of a single passageway that follows the coal seam back into the mountain. Drift mines eliminate the need to tunnel through overlying rock to reach a coal deposit.
A single underground coal mine may have all three types of passageways (drift, slope, and shaft). For example, miners might dig a drift mine to excavate coal from a hillside outcrop. As the drift mine follows the coal bed into the earth, the miners might dig angled passageways (a slope mine) from above down to the coal bed to shorten the transportation distance into the progressing mine. If the overburden becomes too deep above the progressing mine, the miners may dig more economical vertical passageways (a shaft mine) to provide transportation and ventilation.
Once a coal deposit has been reached by a shaft, slope, or drift mine, workers mine the coal by one of two methods: the room-and-pillar method or the longwall method. Room-and-pillar mines extract coal at greater depths and are usually left standing when the mine is abandoned. Longwall mines are used at shallower depths and are allowed to collapse as the mine progresses.
B.1. Room-and-Pillar Method
As its name implies, the room-and-pillar method uses rows of large pillars of coal to support the roof of a mine. Workers tunnel parallel passageways through the coal seam, and then cut 12- to 24-m (40- to 80-ft) wide pillars at regular intervals out of the separating walls of coal. The percentage of coal recovered from a coal seam mined by the room-and-pillar system depends on the economic incentive to remove as much coal as possible versus the number and size of coal pillars necessary to support the roof. Workers leave the pillars standing in areas where environmental regulations prohibit land subsidence (sinking or settling of land). In areas where land subsidence is acceptable, workers may remove some pillars just before closing the mine.
Miners use two processes, known as conventional mining and continuous mining, to remove coal from room-and-pillar underground mines. Conventional coal mining replaced hand mining (mining with pick and shovel) in the 1930s. In conventional mining, miners use power saws to slice a deep cut, 3 to 4 m (10 to 12 ft) wide, into the bottom of a coal wall. Next, they drill holes into the coal above this cut and fill the holes with explosives. The explosions dislodge chunks of coal from the wall. Conveyors or rubber-tired electric vehicles known as shuttle cars carry the coal chunks out of the mine.
Continuous mining makes use of a machine known as a continuous miner that can be operated by remote control. This mobile machine has a series of metal-studded rotating drums that gouge coal from the face of the coal seam (known as the wall face). One continuous miner can mechanically break apart about 1.8 metric tons of coal per hour. After a wall face has been mined to a certain depth, miners stabilize the adjacent roof by bolting long rods into the mine ceiling, advance the ventilation, and begin a new continuous mining cycle.
Contributed By: James Speight, B.S., Ph.D.
Visiting Professor, Technical University of Denmark. Former Chief Executive Officer, Western Research Institute.
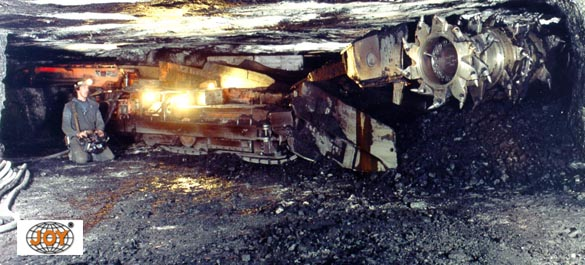
Operator of a continuous miner uses a remote control unit to position himself to the rear of the machine for reduced exposure to coal dust and noise levels.
The bits (seen in the sketch below) are located in the big pointed wheels that are across the top of the machine sticking up in the air. There are many bits in each wheel, and as you can see there are many wheels across the machine. Depending on the type coal being mined the bits will last approximately 24 hours before they are replaced.
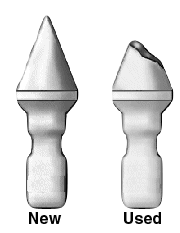
Continuous miners can achieve production rates up to 1,000 tons per shift. The rotating bits on the drum rip the coal from the seam and it is gathered by rotating arms and transported to a haulage vehicle by a chain conveyor.
Continuous miners typically are used for hard to reach small seams of coal using the room pillar method.
B.2. Longwall Mining
Instead of coal pillars, the longwall mining system uses a line of moving hydraulic jacks to support the roof temporarily in the mining area. No coal pillars are present to obstruct work, so a large coal-cutting machine cuts coal continuously along a wall face typically about 180 m (590 ft) wide. This massive coal-cutting machine works like a wood power saw, shredding coal from the wall in strips about 50 to 75 cm (about 20 to 30 in) wide. As the coal-cutting machine strips layers of coal from the wall face like a meat cutter, the line of roof-supporting hydraulic jacks moves automatically behind the machine. As the hydraulic jacks move forward, the roof is allowed to collapse behind the equipment.
Longwall mining produces four to five times more coal from a given deposit than the room-and-pillar method because coal pillars are not built. But because longwall mining causes the land to sink, land use regulations prohibit this practice in many areas. Despite this prohibition, longwall mining still accounts for about 30 percent of the coal mined in the United States.
Contributed By: James Speight, B.S., Ph.D.
Visiting Professor, Technical University of Denmark. Former Chief Executive Officer, Western Research Institute.
“Coal,” Microsoft® Encarta® Online Encyclopedia 2001
http://encarta.msn.com © 1997-2001 Microsoft Corporation. All rights reserved.
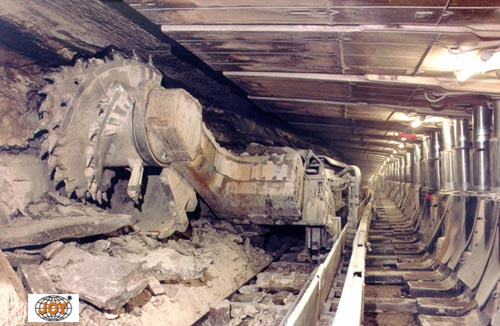
Longwall Mining Machine. Note the hydraulic jacks on the right that are used in this process to support the roof of the mine.
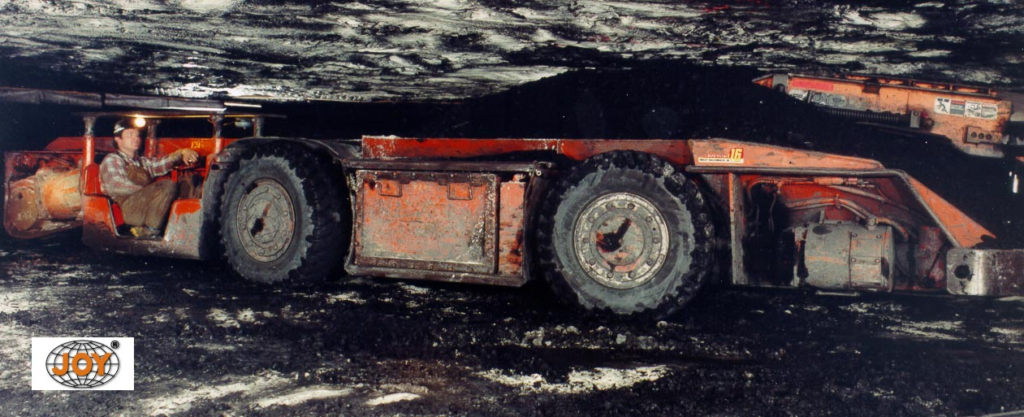
Pictured above is a shuttle car sitting behind a continuous miner taking on a new load of coal. Upon receiving a full load, the shuttle car operator will turn around in his cab and move the vehicle in the opposite direction to transport coal to a central loading point for removal from the mine. If you look closely, you will see the end of a conveyor on the right-hand side just below the roof is filling the shuttle-car with coal. A shuttle-car payload capacity can range from 8.5 – 25 Tons or 7.7 – 22.7 Metric Tonnes, depending on the size of the car.
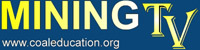
See Modern Mining Machines at work on your own computer. Click on Logo and enjoy.